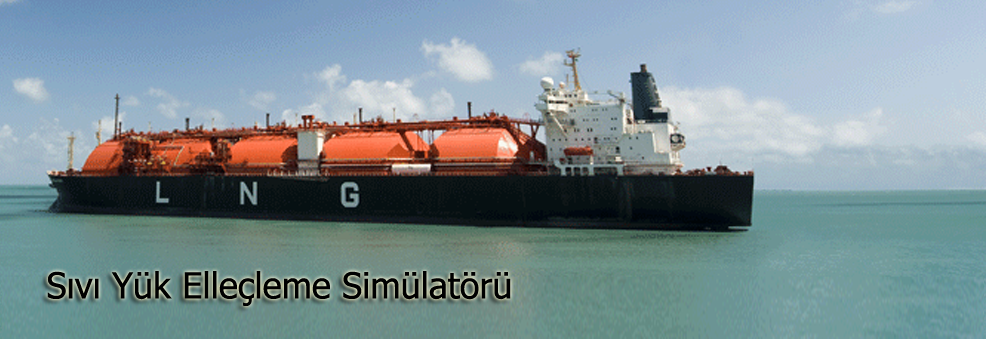
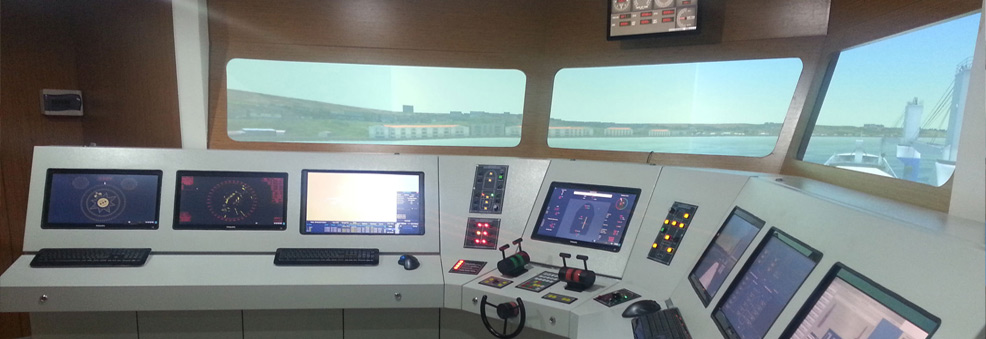
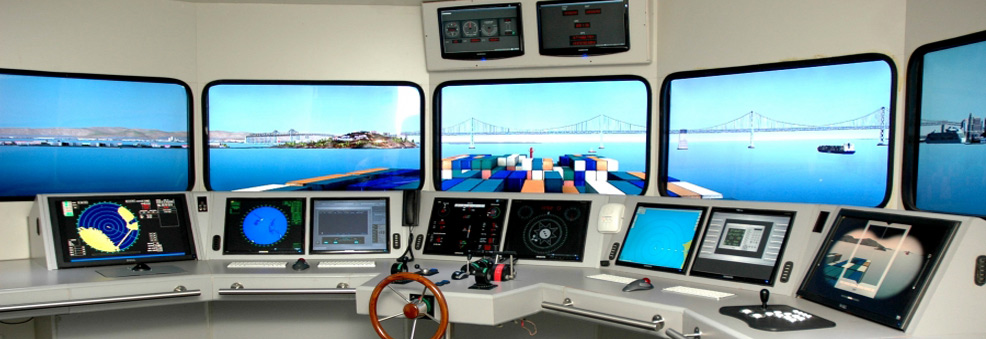
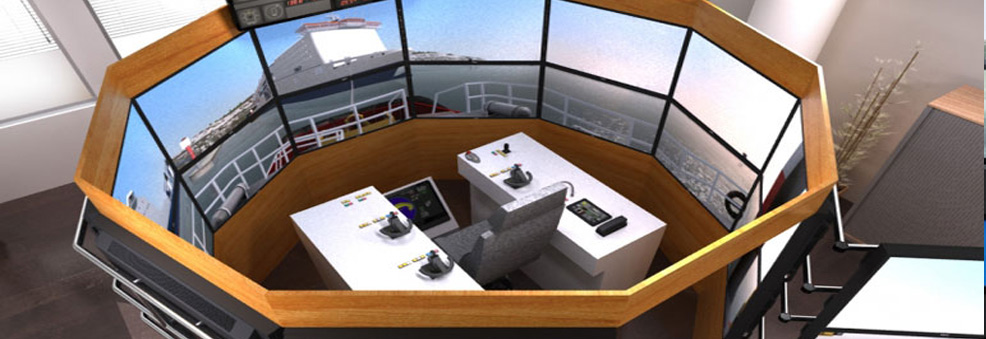
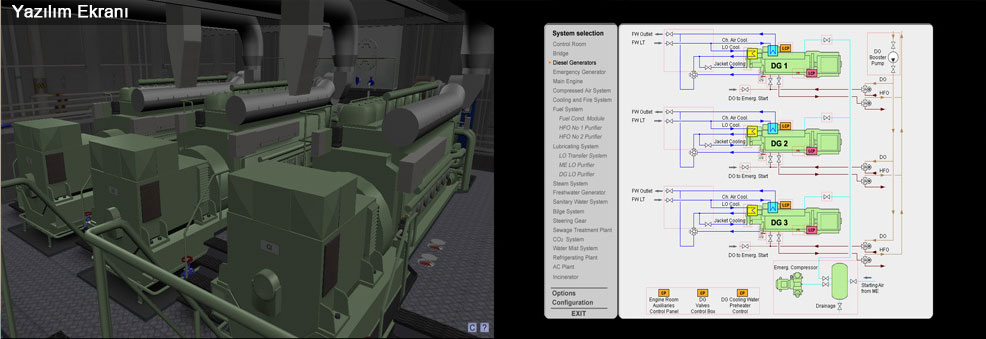
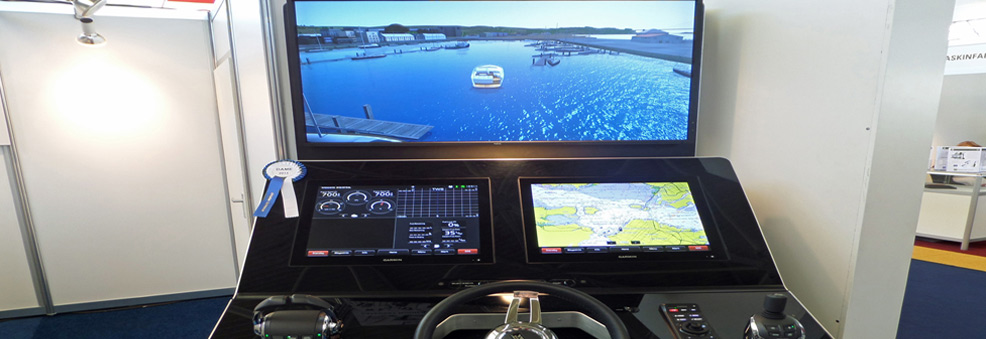
General Features of the LCHS-Liquid Cargo Handling Simulator
The Liquid Freight Handling Simulator is designed for the training and certification of liquid cargo tankers, gas carriers and terminal personnel as well as other personnel responsible for safe cargo loading and operation of auxiliary equipment.
The Liquid Freight Handling simulator provides a full detailed copy (simulation) of ship / terminal systems and partitions.
The Liquid Freight Handling Simulator is the ideal solution for training in training centers, academies, maritime schools, shipping companies, coastal centers.
It includes training parts for replacing liquid cargo tankers and gas carrier ships in a safe and efficient manner. Liquid cargo handling simulator is used for training and practical training of tanker general equipment systems and tanker working principles. Practical training of the system and control of the mechanism can be verified and applied for load handling performance in the emergency station and standard operating conditions. This simulation aims at the operation of tanker systems in line with the requirements of the standard IMO courses.
The Desktop - Liquid Freight Handling Simulator is designed to meet standard trainings with pre-configured exercises on tanker models
Standard training objectives depend on the tanker model, listed below.
- Loading process
- Dumping process
- Ballasting operation
- Ballast water disposal operation
OIL TANKER (AFRAMAX)
In this model, 105,000 Mt DWT crude oil carrier model is taken as an example.
Its main components are:
1- 6 double cargo tanks and 1 double slot tank
2- 6 separated ballast tanks with separated ballast system and top stores
LPG CARRIER – FULLY REFRIGERATED LARGE LPGC (VLGC)
In this model, a fully cooled gas carrier model with a capacity of 78,000 m3 is taken as an example.
The main components are:
1- 4 Prismatic Cargo Tanks Type A
2- Re-liquefaction systems with independent two-stage seawater cooled sub-system
3- Ballast system
4- Pumps are submerged, electrically operated, centrifugal and equipped with appropriate controls.
LNG Carrier (MOSS)
- LNG Model (MOSS) IGC code based on the specified type 2G ship, vapor pressure suitable for transporting LNG up to 0.25 bar g.
- Cargo Tank without dome cavity capacity:
Cryogenic condition 141,000 m (-100% complete at -1630 C at atmospheric pressure)
Cryogenic condition 138,900 m (-1630 C, filling atmospheric pressure 98.5%)
- 4 pieces Cargo tank - IMO maximum permissible safety valve setting: 0.25 Bar G
- Cargo pumps: 8 x 1,500 m3 / h at 155 MLC (SG 0.5)
Liquid Cargo Simulator - Single Monitored Desktop Version
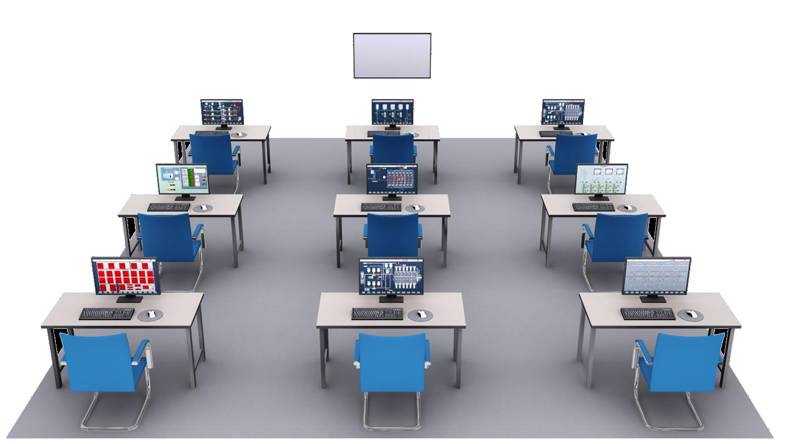
Liquid Cargo Simulator - Desktop Edition with Dual Monitor
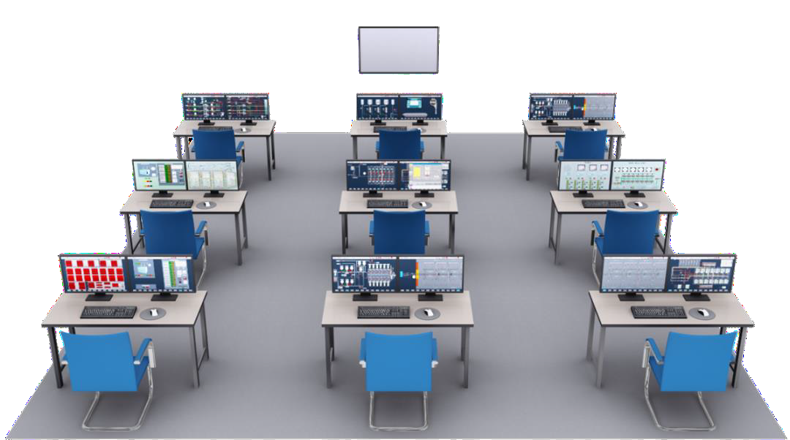